Heavy-Duty Structure Cleaning with Shot Blasting Machines for Industrial Projects
- Riya Singh
- Jan 25
- 13 min read
Updated: Feb 5
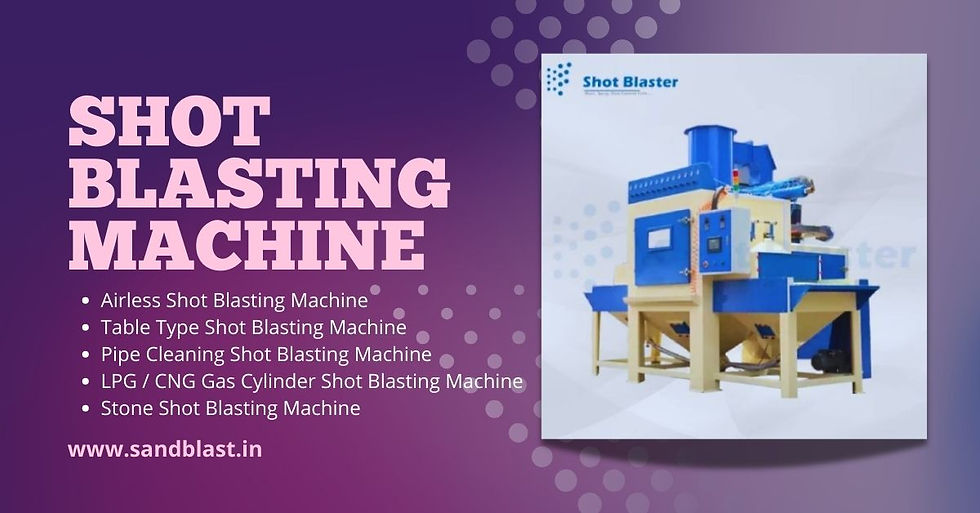
Heavy-duty structure cleaning is significant for various industrial projects. One prevalent method for cleaning metal surfaces involves shot blasting machines. These machines propel small metal balls, known as shot, to eliminate rust, dirt, and old paint from structures. This technique enhances surface smoothness and prepares them for new coatings. It is efficient and can reduce expenses and time in maintaining large equipment and buildings.
Let's examine how shot blasting machines operate and their advantages for the industry.
Importance of Heavy-Duty Structure Cleaning in Industrial Projects
Heavy-duty structure cleaning is vital for safety and integrity in industrial projects. Shot blasting machines provide an effective method to remove rust, contaminants, and old paint from surfaces, which is necessary for precise machining of structural and plate steel. This cleaning method uses blast media in a continuous process, ensuring surfaces are prepared for effective surface finishing.
Without proper cleaning, issues like deburring and descaling can lead to weak spots in materials, impacting the strength and durability of the equipment. Neglecting this can also increase operational costs due to unexpected repairs and longer project timelines from delays.
Process monitoring during shot blasting helps maintain quality, especially with complex geometries and plastic workpieces. Turbine blasting and blast wheels used in the machines allow for efficient coverage, keeping maintenance costs down while extending the service life of industrial structures.
Also Check - Shot Blasting Machine | Shot Blasting Machine Manufacturer | Buy Shot Blasting Machine | Shot Blasting Machine Price | Best Shot Blasting Machine | Shot Blasting Machine Supplier
Overview of Shot Blasting Machines for Industrial Projects
Shot blasting machines are designed for surface finishing and provide significant benefits in industrial settings. They are widely used for deburring and descaling, ensuring that metal surfaces, such as structural and plate steel, are clean and smooth. During the shot blast process, these machines use blast media to remove rust, paint, and other unwanted materials from workpieces. This cleaning helps prepare heavy-duty structures for painting or coating.
Different types of shot blasting machines, like turbine blasting systems, are specialized for various applications. For instance, machines can be tailored to handle complex geometries or plastic workpieces, allowing for precise machining. The use of blast wheels helps ensure an even distribution of blast media, which supports efficient surface treatment.
Additionally, process monitoring is often part of modern machines, allowing operators to keep track of the blasting process and make adjustments as needed for superior results in their projects.
Types of Shot Blasting Machines
Belt Blast Machines
Belt Blast Machines offer significant operational benefits for surface finishing tasks, especially when working with complex shapes of plastic components and structural steel. These machines facilitate a continuous process, ensuring efficient shot blasting, deburring, and descaling. Their innovative design features blast wheels strategically positioned to distribute blast media evenly over the workpiece, improving effectiveness in machining operations.
With shot peening capabilities, they provide accurate machining and optimal surface treatment of plate steel. Regular maintenance of blast wheels and ongoing process monitoring are advised to sustain performance and durability.
Operators should also execute regular cleaning to avoid debris accumulation and maintain consistent functionality. This upkeep not only extends the machine's lifespan but also enhances quality results in the surface treatment of various materials.
Multi-Tumbler Solutions
Multi-Tumbler Solutions enhance the efficiency of shot blasting processes in industrial applications. They facilitate the continuous process of surface finishing, simplifying the handling of various machining tasks such as deburring, descaling, and shot peening. These machines are adept at processing different materials, including structural and plate steel, and can manage complex shapes or plastic components.
Unlike other shot blasting machines, Multi-Tumbler Solutions are recognized for their versatility and performance, featuring adjustable blast wheels for optimal media use. This improves process monitoring and ensures precise machining. Furthermore, sectors like automotive and aerospace experience significant gains from Multi-Tumbler Solutions, boosting both product quality and overall production efficiency.
Tumble Belt Blast Machines
Tumble Belt Blast Machines are designed for effective surface finishing and specialize in handling complex geometries and various workpieces, including structural and plate steel. They provide a continuous process of shot blasting, ensuring consistent and efficient cleaning of heavy-duty structures. With their blast wheels and process monitoring features, they deliver an even distribution of blast media, allowing for precise machining and effective deburring and descaling.
These machines excel in industries like automotive and aerospace, where maintaining high cleaning and surface treatment standards is necessary. Tumble Belt Blast Machines can also accommodate plastic workpieces, ensuring versatile applications across different materials while achieving excellent results in shot peening and other machining processes.
Read Another Article -https://riyasingh12384.wixsite.com/shotblaster/post/next-gen-automatic-shot-blasting-machines-for-precision-surface-preparation
Key Features of Shot Blasting Machines
Durability and Reliability
To ensure the long-term durability of shot blasting machines in industrial applications, regular maintenance is necessary. This includes inspections of blast wheels and turbines to prevent wear and tear. Using appropriate blast media for various materials, such as structural steel or plastic workpieces, enhances the longevity of machines. The reliability of shot blasting machines directly affects the efficiency of industrial cleaning processes.
Consistent performance in surface finishing tasks like deburring and descaling improves productivity and reduces downtime. When evaluating durability and reliability, factors like the machine’s design for complex geometries, the robustness of machining processes, and process monitoring capabilities should be considered. Machines that specialize in turbine blasting, for example, offer precise machining for challenging projects.
By taking these steps and considering these factors, companies can ensure that their shot blasting operations remain efficient and effective over time.
Versatile Applications in Manufacturing
Versatile applications in manufacturing improve operational efficiency across various industrial sectors by allowing for the effective treatment of materials such as structural steel and plate steel. Shot blasting machines provide several advantages; they enhance surface finishing through processes like deburring, descaling, and shot peening. This occurs continuously, ensuring high-quality results without slowing production.
The shot blast technique employs blast wheels to propel blast media against workpieces, making it suitable for complex geometries and precise machining. Manufacturers appreciate this adaptability, as shot blasting machines can be customized to meet different needs, handling everything from plastic items to metal components.
Additionally, process monitoring capabilities enable operators to adjust parameters in real-time, ensuring that each task meets the required specifications. Integrating shot blasting not only streamlines production but also supports a variety of machining processes, making it a flexible solution in modern manufacturing.
Also Check - https://cutt.ly/Re9OXAD3 | | https://shorturl.at/zeKzq | https://shorturl.at/oPRgI | https://rb.gy/sljqqa
Advantages of Using Shot Blasting in the Manufacturing Industry
Improved Surface Quality
Improved surface quality is reached through various factors in shot blasting techniques for industrial projects. Shot blasting machines are designed to perform processes like deburring, descaling, and shot peening, which help refine material surfaces. The selection of specific machines, such as turbine blasting units equipped with blast wheels, ensures that the right blast media is used to treat complex geometries or plastic workpieces effectively.
This tailored approach enhances the overall surface finish of materials like structural steel and plate steel. A continuous process allows for consistent process monitoring, ensuring that each batch maintains high standards. When surface quality improves, it directly affects the longevity and performance of manufactured products, as smoother surfaces reduce wear and tear over time. In industries where precise machining is necessary, achieving a refined surface is significant for maintaining the integrity and function of components.
Cost-Effective Solutions for Industrial Projects
Cost-effective solutions for industrial projects using shot blasting machines involve several factors. Companies should consider the type of blast media, as it can greatly affect both the cost and effectiveness of the surface finishing processes. When selecting machines, organizations can optimize budgets by choosing equipment that is specialized for their needs, such as turbine blasting for structural steel or plate steel, which may require less maintenance and provide better durability.
Innovative advancements like improved blast wheels and process monitoring systems allow for precise machining, making it easier to handle complex geometries and plastic workpieces.
Additionally, efficient techniques such as descaling and deburring are incorporated into a continuous process that reduces time and minimizes waste. By embracing new technologies and practices, companies can achieve better results while keeping operational costs down, making shot blasting an effective choice for various machining processes.
Considerations When Selecting a Shot Blasting Machine
Choosing the Right Machine Manufacturer
When considering machine manufacturers for shot blasting machines, companies should assess the manufacturer's experience and reputation in the industry. A manufacturer that focuses on surface finishing and has a solid history is more likely to offer dependable products, such as machines for shot peening or turbine blasting. Reviewing customer testimonials and case studies related to deburring or descaling can provide valuable insight into their expertise.
To evaluate if a manufacturer offers sufficient support, companies can ask about their process monitoring systems and availability of service for maintenance after purchase.
A reliable manufacturer typically shares examples of response times and customer service history. Furthermore, assessing the quality and durability of machines involves looking at the materials used, such as blast wheels made for demanding applications, and how they perform with various blast media.
Testing machines on components like structural steel and plate steel, particularly those with intricate shapes, ensures precise machining that aligns with industry standards, affirming the manufacturer's commitment to quality.
Assessing Individual Project Requirements
When assessing individual project requirements for "shot blasting machines", specific project goals and outcomes must be defined. This includes determining the type of surface finishing needed, such as deburring or descaling, and whether shot peening is required for structural steel or plate steel.
Unique environmental conditions at the project site can influence the choice of blasting equipment; for example, areas with limited space might require machines with compact designs or specialized adaptations for complex geometries. A project with continuous processes may benefit from turbine blasting systems with blast wheels that enhance efficiency.
Factors like project scale and budget are also important; larger projects may require robust machines with higher capacities and more advanced process monitoring features, while smaller projects could focus on cost-effective solutions with lower operating costs.
Choosing the right blast media for plastic workpieces versus metals is another consideration that affects both performance and expenses. The overall strategy should align all these elements to meet precise machining standards effectively.
Applications of Shot Blasting in Different Industries
Use in Construction and Infrastructure Projects
Shot blasting machines serve a significant function in surface finishing for construction and infrastructure projects. They prepare surfaces by eliminating rust, old paint, and other contaminants, which improves adhesion for coatings. When selecting shot blasting equipment, it is important to consider factors like the type of blast media, machine capacity, and the ability to manage complex geometries, such as plastic workpieces or structural steel.
The choice of blast wheels and turbine blasting options can also influence the process's efficiency. Shot blasting accelerates these processes through continuous operation while enhancing deburring and descaling. Monitoring the process effectively can minimize waste, making projects more cost-efficient. By enabling precise machining, shot blasting machines boost the overall quality of finished surfaces, contributing to safer and more durable infrastructure.
Applications in Aerospace and Automotive Manufacturing
Shot blasting is a method that improves surface preparation for aerospace and automotive manufacturing. It provides benefits like deburring, descaling, and surface finishing, ensuring that materials such as structural steel and plate steel are ready for coating or assembly. Shot blasting machines use blast wheels to shoot blast media at the surfaces of plastic workpieces or metal parts, ensuring precise machining, even on complex geometries.
Advancements in technology enhance these processes, leading to better designs that are lighter and stronger. Newer machines allow for more efficient turbine blasting and improved process monitoring, helping manufacturers keep track of their operations.
Automation and Industry 4.0 techniques can also make shot blasting more effective by streamlining the production line. With automated systems, manufacturers can achieve a continuous process that reduces downtime and increases output.
More from this category - https://riyasingh12384.wixsite.com/shotblaster/post/automatic-shot-blasting-solutions-for-the-automobile-industry
Future Trends in Shot Blasting Machines for Industrial Projects
Advancements in Blast Machine Technology
Recent advancements in shot blasting machines greatly enhance efficiency and effectiveness in industrial applications. Modern machines feature improved blast wheels that allow for accurate shot blast operations on complex geometries, including plastic workpieces and structural steel. These upgrades provide better surface finishing, deburring, and descaling, which are significant processes in machining.
The continuous process capabilities enable quick adjustments and process monitoring for optimal performance. Innovations also focus on sustainability; for example, the use of eco-friendly blast media reduces waste and energy consumption, helping manufacturers address environmental concerns. Furthermore, automation integration in these machines aligns with Industry 4.0, streamlining operations and ensuring more precise machining. This trend allows for real-time data tracking and adjustments, boosting overall productivity and minimizing human error.
As shot blasting technology evolves, it brings together efficiency, sustainability, and smart manufacturing for modern industrial projects.
Integration with Automation and Industry 4.0
The integration of shot blasting machines with automation technology enhances operational efficiency by allowing for continuous processes in surface finishing. Automation enables precise machining of complex geometries, ensuring that every surface treatment, such as deburring or descaling, is performed consistently.
With the push towards Industry 4.0, shot blasting machines can benefit from real-time monitoring and data collection, helping operators track the performance of blast wheels and blast media. This facilitates easier adjustments for structural steel and plate steel, leading to improved quality. Smart technologies, like sensors and AI, further streamline shot blasting processes by analyzing data for better decision-making.
This translates to faster shot peening effects and less downtime, all while maintaining high standards of surface treatment for both metal and plastic workpieces.
As a result, production lines become more efficient and reliable.
Also Check - https://rb.gy/ii4tpg | https://rebrand.ly/SB5asln | https://rebrand.ly/SB49Ind | https://cutt.ly/Ge9OZ25U
Selecting the Right Solutions for Your Project
Integration with Wire Mesh and Other System Components
Incorporating wire mesh into shot blasting operations can greatly improve efficiency in surface finishing. By employing wire mesh to support the flow of plastic workpieces or structural steel, shot blasting machines can effectively process intricate shapes. When connecting a shot blasting machine with other parts, it is important to ensure correct alignment and flow of blast media throughout the system.
This facilitates deburring and descaling, which are necessary for maintaining a high-quality surface finish. The compatibility between wire mesh and shot blasting machines also influences overall performance, as it enables precise machining techniques.
For example, using turbine blasting with optimized blast wheels minimizes wear and tear, resulting in a longer lifespan for both the machines and wire mesh systems. Furthermore, process monitoring can be improved when both components operate harmoniously, ensuring that every stage of shot peening functions effectively and contributes to a more efficient workflow in industrial projects.
Evaluating Automatic technologies for Optimal Performance
When evaluating the performance metrics of different shot blasting machine technologies, factors such as surface finishing, deburring, and descaling should be considered. The reliability and efficiency of shot blasting solutions depend on the effectiveness of blast wheels and the type of blast media used. For instance, when handling complex geometries and plastic workpieces, precise machining becomes important.
Innovations in technologies like turbine blasting and shot peening can significantly enhance the continuous process of surface treatment, leading to improved productivity in machining processes. Process monitoring systems can also be integrated to better manage these operations.
Expert Tips for Effective Use of Shot Blasting Machines
1. Regular Maintenance of Machines
Regular maintenance of shot blasting machines is necessary for extending their operational lifespan and ensuring efficiency. Operators should follow a routine maintenance schedule that includes daily checks of blast wheels, which are important for effective surface finishing. Weekly inspections might cover the condition of the blast media used in turbine blasting and the effectiveness of deburring and descaling processes.
For monthly maintenance, operators should focus on process monitoring systems that help detect any irregularities. Including checks for wear on complex geometries and ensuring the machines can handle various materials, like structural steel or plastic workpieces, should also be prioritized.
Implementing this schedule minimizes downtime and boosts productivity in industrial projects by enabling timely repairs and adjustments.
Safety inspections should not be overlooked, focusing on machine guards and safety features, allowing workers to operate shot blasting machines confidently and effectively.
2. Proper Training for Operators
Operators should acquire several competencies and skills through proper training to effectively use shot blasting machines. They need to understand the different types of blast media and their applications for surface finishing and deburring on materials like structural steel and plate steel. Training should also cover the operation of blast wheels and turbine blasting techniques, particularly for processing complex geometries and plastic workpieces.
Ongoing training enhances safety and efficiency by keeping operators informed about proper process monitoring and risk management during the shot blasting process. Regular workshops and refresher courses, incorporating hands-on experience, help ensure operators retain their training knowledge.
Using simulations and practical exercises can effectively demonstrate the significance of maintaining optimal settings for shot peening and descaling.
Lastly, staying updated with advancements in shot blasting technology encourages operators to engage in continuous learning, ensuring they remain well-versed in the latest machining processes to maximize the effectiveness of the machines they operate.
3. Understanding Material Compatibility
When evaluating material compatibility for shot blasting machines, various factors must be considered, such as the type of blast media and the material characteristics of the workpieces.
For example, structural steel and plate steel can endure higher blast pressures compared to plastic workpieces, particularly in complex geometries. Recognizing this compatibility can greatly influence surface finishing, ensuring that shot blasting, shot peening, and deburring processes operate effectively.
It contributes to the longevity of the machines and the quality of the finishes. Using incompatible materials may result in equipment damage, poor surface quality, and higher costs. Insufficient process monitoring can lead to undesirable outcomes like descaling failures or ineffective machining.
Selecting the appropriate blast wheels for turbine blasting, customized for the specific materials, enhances performance and improves the overall effectiveness of surface treatment processes.
Wrapping up
Heavy-duty structure cleaning is important for industrial projects to maintain equipment integrity and enhance operational efficiency. Shot blasting machines emerge as a powerful solution for this purpose. These machines employ high-velocity steel shots or abrasive materials to remove contaminants such as rust, paint, and debris from surfaces.
Shot blasting offers several advantages, including improved surface preparation for painting and coating applications, which extends the lifespan of industrial structures. The process is efficient, allowing for quick turnaround times while reducing labor costs. Additionally, it is environmentally friendly compared to chemical cleaning methods, as it generates minimal waste and does not use harmful solvents.
Different types of shot blasting machines are available, including tumble blast, wheel blast, and automated systems, each suited for specific cleaning needs. Safety measures should be implemented to protect workers from dust and noise hazards associated with the blasting process.
FAQs on heavy-duty shot blasting machines
What are shot blasting machines, and how do they work for heavy-duty structure cleaning?
Shot blasting machines are heavy-duty tools that use high-speed steel shots to clean and prepare surfaces. They effectively remove rust, scale, and contaminants from structures like bridges and ships, ensuring excellent adhesion for coatings. Examples include tumble blast and wheel blast machines for various cleaning needs.
What types of surfaces can be effectively cleaned using shot blasting machines in industrial projects?
Shot blasting machines effectively clean a variety of surfaces, including concrete, metal, and stone. They are ideal for removing rust from steel beams, degreasing machinery parts, and preparing concrete floors for coating or sealing.
What are the advantages of using shot blasting for heavy-duty cleaning compared to other methods?
Shot blasting offers superior efficiency and thoroughness for heavy-duty cleaning, effectively removing rust and contaminants in less time. Unlike chemical methods, it’s eco-friendly and requires no hazardous materials. For example, it quickly prepares metal surfaces for painting or coating, ensuring better adhesion and durability.
How do I determine the right shot blasting machine for my specific industrial cleaning needs?
Assess your cleaning requirements by considering factors like part size, material type, and desired finish. For instance, choose a cabinet blaster for small metal parts or a drum blaster for large components. Consult manufacturers’ specifications and industry experts for tailored recommendations.
Are there any safety precautions I should follow while using shot blasting machines for structure cleaning?
Yes, wear appropriate personal protective equipment (PPE) such as helmets, gloves, goggles, and respiratory masks. Ensure proper ventilation in the workspace, maintain a safe distance from bystanders, and regularly inspect equipment for malfunctions. Always follow manufacturer guidelines for operation and safety.
Discover high-quality shot blasting machines that deliver exceptional performance and reliability. Explore the best solutions for surface cleaning on our official website!
ความคิดเห็น